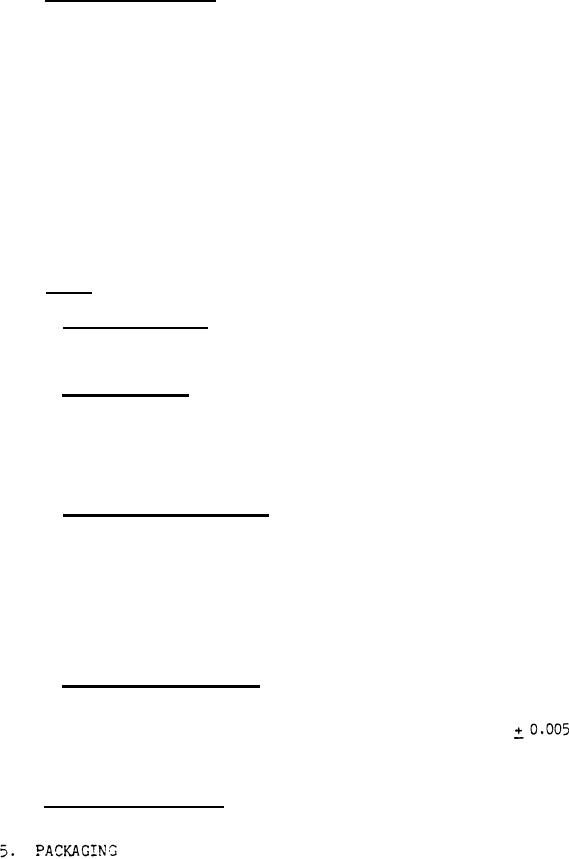
MIL-L-14576F
(a) Product examination (see 4.5).
(b) Tests (see 4.6).
(c) Packaging inspection (see 4.7).
* 4.5 Product examination Visually, dimensionally, and manually examine each item
to determine conformance with the requirements of 3.2 through 3.4.9, 3.5.3 through
3.6.3, and 3.6.4 through 3.12. Visual examinations shall include verification of
completeness of manufacture and assembly, conformance to identified specified
standards, adequacy of markings, proper cleaning, and freedom from defects.
Dimensional examination includes measuring dimensions as specified. Manual
examinations shall include the operation of movable parts by hand to assure proper
functioning. The examination provisions may be applied at the earliest practial
point in manufacture at which it is feasible to inspect for acceptance without risk
of change in the characteristic by subsequent operations. Failure of the contractor
to provide objective evidence that the item and its components have passed the
examinations prescribed for them by the contractor's inspection system shall be
cause for rejection. In addition, failure of the contractor to provide objective
evidence that all parts are manufactured to definite standards, clearances, and
tolerances so that no replacement part will degrade the form, fit, or function of
the end item (see 3.4.3), shall be cause for rejection.
4.6 Tests.
4.6.1 Operational test. The lathe shall be operated at no load to determine
proper operation of all controls, motors, adjusting mechanisms, and other
accessories.
* 4.6.2 Alignment test. A cylindrical test mandrel, no less than 10 inches long,
shall be mounted in the headstock and tailstock chucks. Dial indicators shall be
mounted to the saw fixture and tool post. The fixture and post shall then be
traversed a distance of no less than 2.5 inches along the mandrel to measure the
vertical and horizontal alignment. A variation in either horizontal or vertical
alignment of 0.002 inch or greater shall be cause for rejection (see 3.6.3. I).
* 4.6.3 Commutator turning test. The lathe must have passed the tests of 4.5.1 and
4.6.2 before performing this test. The test shall be performed on a motor or
generator armature having a commutator no less than one inch in diameter, nor less
than an inch in length. The operator shall take a series of cuts to reduce the
commutator diameter by at least 0.025 inch over the full length of the commutator.
The turned surface finish shall be not more than 63 microinches arithmetic average
(aa), in accordance with ANSI B46.1. Variation in concentricity of the finished
commutator shall not exceed 0.0005 inch total indicator reading. Taper shall not
exceed 0.005 inch per linear inch of the turned surface (see 3.5.1).
4.6.4 Mica undercutting test. Following completion of the test in 4.6.3, the
sample lathes shall be subjected to a mica undercutting test. While the armature is
still in the lathe, the operator shall use the mica undercutting device to undercut
the mica between the commutator bars to a depth of 0.0313
inch. The
undercut shall be uniform in depth within + 0.005 inch for its full length and width
(see 3.5.2).
4.7 Packaging inspection. Packaging inspection shall be conducted before and
after packaging to determine compliance with the requirements of' Section 5.
For Parts Inquires call Parts Hangar, Inc (727) 493-0744
© Copyright 2015 Integrated Publishing, Inc.
A Service Disabled Veteran Owned Small Business